Diagnosing P0336 Crankshaft Position Sensor A Circuit Range Performance Issues’
P0336 is an OBD-II diagnostic trouble code (DTC) associated with a malfunction in the crankshaft position sensor circuit. This code typically indicates that the crankshaft position sensor (CKP) is not functioning correctly, and is not sending a signal to the powertrain control module (PCM). The CKP monitors the rotational speed of the crankshaft, and sends this information to the PCM so that it can adjust ignition timing and fuel delivery accordingly. If the CKP is malfunctioning, it may cause poor engine performance, a decrease in fuel economy, and even stalling. To diagnose this code, a technician will first inspect all wiring and connectors associated with the CKP. They will then perform tests on the CKP to make sure it’s working properly. If all these checks out, then they may need to replace or repair other components such as the PCM or camshaft position sensor.
Automobile: P0336 Crankshaft Position Sensor A Circuit Range Performance
Overview of the Crankshaft Position Sensor
The crankshaft position sensor is a vital part of the automotive engine management system. It is used to measure the position and speed of the crankshaft, which in turn helps to determine the timing of fuel injection and ignition. The crankshaft position sensor is usually located on the side of the engine block, near the crankshaft pulley. It consists of two parts: an electronic circuit board and a magnetic pickup coil. The electronic circuit board contains components that detect changes in the magnetic field generated by the coil, which in turn provide information about crankshaft position and speed.
Common Symptoms of a Faulty Crankshaft Position Sensor
When a crankshaft position sensor fails, it can cause a variety of problems with an engine’s performance. Common symptoms include misfires, stalling, hard starting, poor acceleration, rough idle, and hesitation when accelerating. Other symptoms may include excessive vibration or knocking noises coming from the engine compartment or a check engine light illuminated on your dashboard.
Causes of a Faulty Crankshaft Position Sensor
There are several common causes for a faulty crankshaft position sensor including wiring harness problems (corrosion or damage), electrical issues (shorted circuits or power loss), and physical damage (cracked circuit board or broken wires). Other causes can include mechanical problems such as worn bearings or internal failure due to overheating.
Diagnosis of a Faulty Crankshaft Position Sensor
When diagnosing a faulty crankshaft position sensor it is important to first check for electrical problems such as wiring harness corrosion or damage and inspect for any shorts in the system. If no electrical issue can be found then you should examine the output from the sensor itself by performing voltage tests at each connector terminal with a multimeter. This will help determine if there is an issue with either power supply to the connector or with one of its output signals.
How to Troubleshoot and Diagnose a Faulty Crankshaft Position Sensor
The first step in troubleshooting and diagnosing a faulty crankshaft position sensor is to conduct a visual inspection of both its connectors and wiring harnesses for any signs of corrosion or damage that may be causing an issue with its operation. Additionally you should perform multimeter tests on each connector terminal for voltage readings as this will help identify if there is an issue with either power supply to it or one of its output signals. If no electrical issues can be found then you should proceed to testing its operation with an oscilloscope as this will allow you to view its output waveform which can help determine if there are any issues with it’s internal components such as circuit board failure due to overheating.
Testing the Crankshaft Position Sensor
Before replacing your crankshaft position sensor it is important that you test it first using both visual inspection techniques and multimeter tests on each connector terminal for voltage readings as this will allow you to identify any potential electrical issues that could be causing your problem before replacing unneeded parts unnecessarily. Additionally, if you have access to an oscilloscope then it would be beneficial for you to use this tool so that you can view its output waveform which could help diagnose any internal component failures such as circuit board damage due to overheating before replacing unneeded parts unnecessarily again.
Replacing a Faulty Crankshaft Position Sensor
Replacing your faulty crankshaft position sensor involves several steps including removing existing part from vehicle; cleaning up area; placing new part into location; connecting wiring harnesses; fastening bolts/nuts; testing new part; reinstalling components; retesting new part; reapplying sealants/antifreeze/oil; reconnecting battery terminals; starting vehicle; verifying proper operation; road testing vehicle; adjusting idle RPMs (if necessary); resetting fault codes (if necessary); and reinstalling car coverings/panels if applicable). When installing your new crankshaft position sensor it is important that all connections are made correctly otherwise it could cause further issues down the line so make sure all connections are secure before starting your vehicle back up again after installation has been completed successfully!
Common Replacement Parts for a Faulty Crankshaft Position Sensor
When replacing your faulty crankshaft position sensor there are two main types available: Original Equipment Manufacturer (OEM) parts and aftermarket parts which offer different levels of quality but many times at lower prices than OEM counterparts depending on where they are purchased from online or locally near you so make sure do some research before purchasing replacement parts! OEM replacement parts typically offer higher quality but will cost more than aftermarket counterparts while also having longer warranty periods associated with them so keep these things in mind when making your decision based off budget needs versus quality needs when selecting replacement parts!
Safety Tips When Working with Automobile Electrical Systems
It is important to take safety precautions when working with automobile electrical systems. Certain tools and materials can cause serious injury if used improperly. Before beginning any work on an automobile electrical system, make sure you are wearing safety glasses, gloves, and other protective clothing. It is also important to have a fire extinguisher on hand in case of an emergency.
Never attempt to work on an automobile electrical system unless you understand the basics of electricity and how it works. You should also be aware of the specific requirements for each type of system in order to make sure that all connections are properly made. This includes being aware of any safety hazards associated with the particular system you are working on.
When working on an automobile electrical system, always disconnect the negative battery cable first before attempting any repairs or modifications. This will prevent accidental short circuits from occurring which could damage sensitive components or cause serious injury or death. After disconnecting the negative cable, turn off all ignition sources such as the key switch or starter relay. Finally, make sure that all tools and materials are properly insulated in order to prevent shock or electrocution when handling live wires and components.
Basics of Working with Automobile Electrical Systems
Understanding the basics of how automobile electrical systems work is essential for anyone who wishes to work on them safely and effectively. Automotive wiring systems typically consist of a battery, alternator, starter motor, spark plugs, distributor cap, and various sensors that control engine performance such as oxygen level sensors and a crankshaft position sensor (P0336).
The most important part of any automobile electrical system is the battery which supplies power to all other components. It is important to keep this component charged up at all times in order to ensure proper operation of all other components in the system such as lights, radio, air conditioner etc.. The alternator is responsible for recharging the battery while the engine is running by drawing power from it then converting it into DC current which can be used by other components in the car.
The starter motor is responsible for turning over the engine when it is first started up and must be kept in good condition at all times in order for your car to run smoothly. The spark plugs are responsible for providing combustion by igniting fuel vapors inside the cylinders while distributor cap ensures that each cylinder receives its own spark plug at exactly the right time during each revolution cycle. Finally, sensors such as oxygen level sensors (O2S) and crankshaft position sensors (P0336) help control engine performance by monitoring vital parameters such as air-fuel ratio and crankshaft rotational speed respectively.
Conclusion
Working with automobile electrical systems can be dangerous if not done correctly so it’s important to understand basic safety precautions before attempting any repairs or modifications yourself. Make sure that you know how electricity works so you don’t cause harm to yourself or damage sensitive components while working on your car’s electrical system. Also understanding how different components like batteries, alternators, starter motors etc… operate will help you diagnose problems quickly without having to guess what might be wrong with your vehicle’s electrical systems
FAQ & Answers
Q: What is a Crankshaft Position Sensor?
A: A crankshaft position sensor is an electronic device that is used to measure the rotational speed and position of the crankshaft in an internal combustion engine. It sends signals to the ignition system, fuel injection system, and other related modules to ensure that the engine runs at optimal performance.
Q: What are the symptoms of a faulty Crankshaft Position Sensor?
A: Common symptoms of a faulty crankshaft position sensor include engine misfires, hard starting, stalling, rough idling, and decreased fuel efficiency. If left unchecked, it can lead to serious engine damage.
Q: How do I test a Crankshaft Position Sensor?
A: To test a crankshaft position sensor, you should first visually inspect the connectors and wiring for any corrosion or damage. Next, you should use a multimeter to check for voltage readings on the connector terminals. If any of these tests fail, it’s likely that the crankshaft position sensor has failed and needs to be replaced.
Q: What are common replacement parts for a faulty crankshaft position sensor?
A: Common replacement parts for a faulty crankshaft position sensor include OEM (Original Equipment Manufacturer) and aftermarket parts. OEM parts are generally more expensive than aftermarket parts but are more reliable and last longer. It’s important to compare prices between OEM and aftermarket parts before making your purchase decision.
Q: What precautions should I take when working with automobile electrical systems?
A: It is important to take certain precautions when working with automobile electrical systems such as wearing protective clothing and eyewear, disconnecting the battery before beginning work on the vehicle’s electrical system, never touching exposed wires or terminals with bare hands or tools, always using insulated tools when working on live circuits, and never attempting repairs outside of your skill level or expertise.
In conclusion, the P0336 Crankshaft Position Sensor A Circuit Range Performance is an important part of an automobile’s engine. It is responsible for monitoring the position of the crankshaft and sending signals to the engine control module (ECM) when it detects a discrepancy. Proper diagnosis and repair of this component are essential to ensure proper functioning of the automobile’s engine.
Author Profile
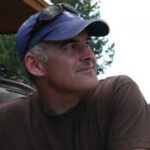
-
With more than 30 years in the bicycle industry, I have a strong background in bicycle retailing, sales, marketing and customer service. I have a passion for cycling and a dedication to excellence. As a manager, I worked diligently to increase my capabilities and responsibilities, managing up to eleven mechanics (at Palo Alto Bicycles) and later as a working partner in my own store.
As the shop owner of Spoke n’ Word Cycles in Socorro, NM, the success of the mission was my responsibility, which I pursued passionately since we opened in 2003 through the spring of 2011. I am adept at managing owned and loan inventory, preparing weekly & annual inventory statements, and managing staff. The role as managing partner also allowed me tremendous freedom. I used this personal freedom to become more deeply involved in my own advancement as a mechanic, to spearhead local trail building, and advocating for cycling both locally and regionally.
As a mechanic, I have several years doing neutral support, experience as a team mechanic, and experience supporting local rides, races, club events. I consistently strive to ensure that bicycles function flawlessly by foreseeing issues and working with the riders, soigners, coaches and other mechanics. Even with decades of experience as a shop mechanic and team mechanic, and continue to pursue greater involvement in this sport as a US Pro Mechanic, and UCI Pro Mechanic.
Latest entries
- July 26, 2023BodyFind the Best Grill for Your 2007 Toyota Tacoma – A Complete Guide
- July 26, 2023BodyUpgrade Your Ford Escape with the Best 2008 Grill – Here’s How!
- July 26, 2023Bumper Stickers, Decals And MagnetsBest Chevy 1500 Door Emblem: Upgrade Your Truck with a Stylish Emblem
- July 26, 2023Marker Light AssembliesGive Your 2008 Dodge Dakota a Makeover with the Best Grill Upgrade