How to Remove a Broken Tensioner Pulley Bolt: Step-by-Step Guide
Removing a broken tensioner pulley bolt can be a daunting task since it’s located in a difficult place to access. But, with the right tools and knowledge, you can do it yourself. Here’s how:
1. First, use a ratchet with an extension and socket to try and loosen the bolt. If you are not successful, then you need to move on to the next step.
2. Remove the tensioner pulley by loosening the two bolts located at the top of it. This will give you better access to the broken bolt.
3. Use an impact driver or drill with a reverse bit attached to get under the broken bolt head and break it loose from its threads.
4. Once you have removed the broken bolt, insert a new one into its place and tighten it securely using your ratchet and socket set.
5. Finally, reattach the tensioner pulley back onto its bolts and make sure all connections are secure before starting your engine again.
Tools Needed
When it comes to removing a broken tensioner pulley bolt from an automobile, there are a few tools that you will need. The first is a socket set, which will be used to remove the bolt from the vehicle. You will also need a drill bit, which can be used to create an opening for the extractor kit. Lastly, you will need an extractor kit itself, which is necessary for removing the broken bolt from the vehicle.
Removing the Old Bolt
Once you have all of your necessary tools, it is time to begin removing the old bolt from your vehicle. Start by disconnecting any power sources or hoses that may be connected to the tensioner pulley and then use your socket set to loosen and remove the old bolt. If there is any debris or rust build-up on the bolt head, use an appropriate cleaner and scrub brush to remove it before attempting to loosen it further with your socket set. Once you have successfully removed the old bolt, use your drill bit to create an opening in its place that is suitable for inserting your extractor kit.
Using Your Extractor Kit
Once you have created an appropriate opening with your drill bit, insert your extractor kit into it and begin turning clockwise until you feel resistance. At this point, keep turning until you can feel that the broken piece of metal has been completely extracted from its hole in the vehicle’s frame. Make sure that all of your safety precautions have been taken before attempting this portion of the removal process as it can be dangerous if not done properly. When finished, reattach any power sources or hoses that were disconnected during this process and then re-secure any bolts or screws that were also taken off during this extraction process.
Cleaning Up
After successfully extracting and removing the broken piece of metal from its hole in your vehicle’s frame, use some type of lubricant such as WD-40 around its edges so as to ensure smooth operation when reinstalling a new tensioner pulley bolt into place once again. Finally, make sure that all edges are clean and free of any sharp objects before reinserting a new tensioner pulley bolt back into place in order to ensure proper functioning when driving again in future trips out on roads or highways.
How to Remove Broken Tensioner Pulley Bolt
Removing a broken tensioner pulley bolt can be a difficult task, and it requires some specialized tools and techniques. This guide will provide step-by-step instructions on how to remove a broken bolt from the tensioner pulley.
Cleaning Up the Bolts Holes and Threads
Before attempting to remove the broken bolt, it is important to clean up the bolt holes and threads. This can be done with a wire brush, sandpaper, or emery cloth. Make sure all debris is removed from the area and that the threads are as clean as possible.
Preparing the Extractor Kit
Now that the bolt holes and threads have been cleaned up, the next step is to prepare an extractor kit. An extractor kit typically consists of a drill bit, an extractor screw, and an extractor socket. The drill bit should be slightly larger than the broken bolt so that it can pass through without any problems. The extractor screw should fit into the hole of the broken bolt head snugly while still allowing for removal of debris as needed. Finally, an extractor socket should be used to attach to the end of the extractor screw so that it can be turned with force when necessary.
Drilling Out the Broken Bolt with an Extractor Kit
Once everything has been prepared, it’s time to drill out the broken bolt using your extractor kit. Start by positioning your drill bit in line with the hole in which you’ll be drilling out your broken bolt head. Slowly drill into it until you reach its depth at which point you’ll then use your extractor screw/socket combination to turn it in a counterclockwise direction until it comes out completely from its hole. If done correctly, this should pull out any debris or remnants of your broken bolt from its hole so that you can easily remove what’s left behind without any further issues or complications.
Using Heating and Cooling Methods
In some cases, heating or cooling methods may need to be used in order to help loosen up a stubbornly stuck tensioner pulley bolt before attempting extraction using an extractor kit. If this is required then use either an acetylene torch or an electric heat gun on low heat setting around where you’ll be drilling out your broken bolt head (be careful not to overheat!). You may also need
FAQ & Answers
Q: What tools are needed to remove a broken tensioner pulley bolt?
A: You will need a socket set, drill bit, and an extractor kit to remove the broken tensioner pulley bolt.
Q: How do I remove the broken bolt from the vehicle?
A: First you will need to remove the old bolt, which can be done by using an appropriate socket on your socket set. Once the old bolt is removed, you can then begin cleaning up any holes or threads in the area.
Q: How do I use an extractor kit to remove a broken bolt?
A: The extractor kit should come with specific instructions for removing a broken bolt. Generally, this involves drilling out the broken bolt using the kit’s drill bit and then using one of the extractors included in the kit to pull out what’s left of the broken bolt.
Q: Are there any alternatives to an extractor kit?
A: Yes, there are several alternatives such as heating and cooling methods or exploding methods that can be used instead of an extractor kit. However, these methods should only be attempted by experienced professionals due to their complexity and potential danger.
Q: What type of safety precautions should I take when removing a broken tensioner pulley bolt?
A: It is important to always wear safety glasses when removing a broken tensioner pulley bolt as flying debris can cause permanent eye damage. Additionally, you should take extra caution when using any heating or cooling methods and make sure that you are familiar with any exploding methods before attempting them.
In conclusion, removing a broken tensioner pulley bolt can be a tricky process, but with the right tools and some patience it is possible. Before attempting to remove the bolt, ensure that it is safe to do so as some tensioner pulleys may be pressurized and could cause injury. The main steps for removing a broken tensioner pulley bolt include securing the tensioner pulley with a screwdriver or clamp, drilling into the bolt head, using an extractor to remove any remaining pieces of the bolt, and then replacing the tensioner pulley with a new one. With these steps in mind, anyone can safely and easily remove a broken tensioner pulley bolt.
Author Profile
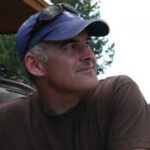
-
With more than 30 years in the bicycle industry, I have a strong background in bicycle retailing, sales, marketing and customer service. I have a passion for cycling and a dedication to excellence. As a manager, I worked diligently to increase my capabilities and responsibilities, managing up to eleven mechanics (at Palo Alto Bicycles) and later as a working partner in my own store.
As the shop owner of Spoke n’ Word Cycles in Socorro, NM, the success of the mission was my responsibility, which I pursued passionately since we opened in 2003 through the spring of 2011. I am adept at managing owned and loan inventory, preparing weekly & annual inventory statements, and managing staff. The role as managing partner also allowed me tremendous freedom. I used this personal freedom to become more deeply involved in my own advancement as a mechanic, to spearhead local trail building, and advocating for cycling both locally and regionally.
As a mechanic, I have several years doing neutral support, experience as a team mechanic, and experience supporting local rides, races, club events. I consistently strive to ensure that bicycles function flawlessly by foreseeing issues and working with the riders, soigners, coaches and other mechanics. Even with decades of experience as a shop mechanic and team mechanic, and continue to pursue greater involvement in this sport as a US Pro Mechanic, and UCI Pro Mechanic.
Latest entries
- July 26, 2023BodyFind the Best Grill for Your 2007 Toyota Tacoma – A Complete Guide
- July 26, 2023BodyUpgrade Your Ford Escape with the Best 2008 Grill – Here’s How!
- July 26, 2023Bumper Stickers, Decals And MagnetsBest Chevy 1500 Door Emblem: Upgrade Your Truck with a Stylish Emblem
- July 26, 2023Marker Light AssembliesGive Your 2008 Dodge Dakota a Makeover with the Best Grill Upgrade