How to Fix a Low Voltage O2 Sensor: A Step-by-Step Guide
A low voltage oxygen sensor is an important component of a car’s emissions system that helps to reduce harmful emissions from the exhaust. If the voltage is too low, the oxygen sensor will not be able to accurately monitor and regulate the air/fuel ratio in the engine, resulting in poor fuel economy and increased emissions. Fortunately, there are several steps you can take to fix a low voltage O2 sensor.
First, make sure that all the components of your vehicle’s exhaust system are connected properly and functioning correctly. Check for any loose connections or clogged filters, as these can cause the O2 sensor to read lower than normal. If necessary, replace any broken or worn parts before continuing with other repairs.
Next, inspect the wiring harness leading to your O2 sensor for any signs of damage or fraying wires. If you find any issues here, it is best to have them fixed by a professional mechanic before attempting to repair the O2 sensor itself.
Finally, if all else fails, try replacing the oxygen sensor itself with a new one from your local auto parts store. Make sure you purchase one that is compatible with your car’s make and model before beginning installation. Once installed correctly according to manufacturer instructions, this should restore proper operation of your vehicle’s emissions system and fix any low voltage issues caused by a faulty O2 sensor.
Automobile: How to Fix Low Voltage O2 Sensor
The oxygen sensor is an essential component of a car’s engine. It measures the amount of oxygen in the exhaust system and sends a signal to the engine control unit (ECU) to adjust the air-fuel mixture. When the oxygen sensor is not working properly, it can cause a variety of problems, including poor engine performance, decreased fuel efficiency, and a lit check engine light. In order to properly diagnose and repair these issues, it is important to understand how to test and replace a faulty oxygen sensor as well as troubleshoot low voltage in an oxygen sensor.
Testing an Oxygen Sensor
Testing an oxygen sensor requires a few steps, including a visual inspection of the area around the sensor, reading diagnostic trouble codes (DTCs), and checking voltage output. During a visual inspection, you should look for any evidence of damage or contamination on the surface of the sensor. These could indicate that there are problems with the wiring or connections that need to be addressed before any further testing can be done.
When reading diagnostic trouble codes, it is important to note any codes related to oxygen sensors as these could indicate that there is something wrong with the sensor itself or its associated wiring or connections. Finally, you should check the voltage output from the sensor using an appropriate multimeter.
Replacing a Faulty Oxygen Sensor
Replacing a faulty oxygen sensor must be done with caution as this component contains hazardous materials that can cause serious injury if mishandled. Before beginning work on your car’s oxygen sensor system, make sure you have all necessary safety equipment such as gloves, goggles and protective clothing.
To replace an old oxygen sensor: locate and remove it from its mounting area; clean and prepare the mounting area; reinstall any components removed during removal; install new sensors according to manufacturer’s instructions; test for proper operation; and finally reconnect all necessary wiring.
Troubleshooting Low Voltage in an Oxygen Sensor
Low voltage output from an oxygen sensor can be caused by several different factors. The most common causes are faulty wiring or connections that have become contaminated over time due to dirt or other debris buildup on the surface of the sensors.
To troubleshoot low voltage output from an oxygen sensor: visually inspect all wiring and connections for signs of damage; clean off any debris build up on both ends of each connection; use an appropriate multimeter to test each connection for proper voltage output; replace any damaged wires or connectors if necessary.
Testing for Low Voltage Output from an Oxygen Sensor
Testing the output voltage of an oxygen sensor is an important step in diagnosing and fixing a vehicle’s engine. The oxygen sensor measures the amount of oxygen in the exhaust and sends a signal to the engine control unit (ECU) to adjust the air/fuel mixture accordingly. If the output voltage is low, it could indicate a faulty oxygen sensor, or other issues with the engine’s performance.
The first step in testing for low voltage output from an oxygen sensor is to check all wiring and connections. If any of the wires are loose or frayed, it could lead to a false reading from the sensor. Additionally, any corrosion on the connectors should be cleaned before testing.
Next, check for any contamination on the surface of the sensor itself. Any dirt or debris that has built up on its surface can cause inaccurate readings. It is also important to make sure there are no cracks or damage to the outer casing of the sensor that could lead to interference with its operation.
Commonly Used Tools for Replacing an Oxygen Sensor
When replacing an oxygen sensor, there are several tools that will be needed in order to complete the job properly and safely. The most common tools required are a ratchet and socket set, an O2 socket wrench, wire cutters, a multimeter, and a vacuum cleaner. Additionally, it is highly recommended that you have anti-seize compound on hand if you plan on reusing your old O2 sensors after installation.
Benefits of Replacing an Oxygen Sensor
Replacing a faulty O2 sensor can have many benefits for your vehicle’s performance and fuel economy. Most noticeably, you should experience improved engine performance as well as better fuel economy due to more accurate readings from your engine control unit (ECU). Additionally, replacing a faulty O2 sensor can help reduce carbon emissions from your vehicle which can help protect our environment in the long run.
Safety Precautions to Take when Working with O2 Sensors
Safety should always be your number one priority when working with any type of automotive part or component – especially when dealing with something as delicate as an oxygen sensor. It is important to wear protective gear such as goggles and gloves while handling these parts in order to protect yourself against any potential hazards such as electrical shocks or chemical spills while working on them. Additionally, exercise caution when working with any electrical components such as wiring harnesses or connectors in order to avoid short circuiting anything during installation or removal processes. Finally, keep away from hot surfaces such as engine blocks or exhaust pipes while working around these areas due to potential burns that could result from contact with them.
Tips For A Smooth Replacement Process
When replacing an oxygen sensor there are several tips that can make sure your job goes smoothly without any hiccups along the way: Make sure all wiring connections are secure before starting work; double check all connections after installation; ensure no debris has been left behind during removal; use anti-seize compound if reusing sensors; always follow safety guidelines when handling automotive parts; read through manufacturers instructions prior to beginning work; test new sensors before putting them into service; be mindful of sharp edges during removal process; replace old gaskets/seals whenever necessary; ensure no leaks exist after installation has been completed; take note of any warning lights present during testing phase after installation has been completed – these could indicate further issue that need attention. Following these tips will help ensure your replacement process goes smoothly without any major issues arising afterwards!
FAQ & Answers
Q: What are the symptoms of a faulty oxygen sensor?
A: Common symptoms of a faulty oxygen sensor include engine performance issues, poor fuel economy, and the check engine light being illuminated.
Q: What tools are needed to replace an oxygen sensor?
A: The tools required for replacing an oxygen sensor include a ratchet and socket set, an O2 socket wrench, wire cutters, a multimeter, a vacuum cleaner, replacement O2 sensor, and anti-seize compound.
Q: What are the benefits of replacing a faulty oxygen sensor?
A: The advantages of replacing a faulty oxygen sensor include improved engine performance, better fuel economy, and reduced carbon emissions.
Q: What safety precautions should be taken when working with O2 sensors?
A: When handling O2 sensors it is important to wear protective gear, exercise caution when working with electrical components, and keep away from hot surfaces.
Q: What tips can help make the replacement process smoother?
A: To ensure a smooth replacement process it is recommended to follow manufacturer instructions closely, double-check all connections before finalizing installation, use anti-seize compound on any threaded connections to prevent corrosion in the future, and clear out any debris from the mounting area before installing the new O2 sensor.
In conclusion, to fix a low voltage o2 sensor in an automobile, the vehicle owner should first check the wiring and connections to the sensor. Make sure all components of the electrical system are functioning properly. If necessary, replace any faulty parts or corroded wires. If that does not fix the problem, it may be necessary to replace the o2 sensor itself. Lastly, if all else fails, consult a certified mechanic for further assistance.
Author Profile
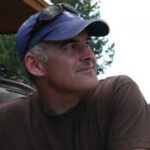
-
With more than 30 years in the bicycle industry, I have a strong background in bicycle retailing, sales, marketing and customer service. I have a passion for cycling and a dedication to excellence. As a manager, I worked diligently to increase my capabilities and responsibilities, managing up to eleven mechanics (at Palo Alto Bicycles) and later as a working partner in my own store.
As the shop owner of Spoke n’ Word Cycles in Socorro, NM, the success of the mission was my responsibility, which I pursued passionately since we opened in 2003 through the spring of 2011. I am adept at managing owned and loan inventory, preparing weekly & annual inventory statements, and managing staff. The role as managing partner also allowed me tremendous freedom. I used this personal freedom to become more deeply involved in my own advancement as a mechanic, to spearhead local trail building, and advocating for cycling both locally and regionally.
As a mechanic, I have several years doing neutral support, experience as a team mechanic, and experience supporting local rides, races, club events. I consistently strive to ensure that bicycles function flawlessly by foreseeing issues and working with the riders, soigners, coaches and other mechanics. Even with decades of experience as a shop mechanic and team mechanic, and continue to pursue greater involvement in this sport as a US Pro Mechanic, and UCI Pro Mechanic.
Latest entries
- July 26, 2023BodyFind the Best Grill for Your 2007 Toyota Tacoma – A Complete Guide
- July 26, 2023BodyUpgrade Your Ford Escape with the Best 2008 Grill – Here’s How!
- July 26, 2023Bumper Stickers, Decals And MagnetsBest Chevy 1500 Door Emblem: Upgrade Your Truck with a Stylish Emblem
- July 26, 2023Marker Light AssembliesGive Your 2008 Dodge Dakota a Makeover with the Best Grill Upgrade