Understanding Fuel Rail Pressure Sensor Circuit Range Performance
The Fuel Rail Pressure Sensor (FRPS) is an important component of a vehicle’s fuel system. It is responsible for measuring and controlling the pressure of fuel within the fuel rail. The FRPS is a type of pressure transducer that converts the pressure of the fuel in the rail into an electrical signal that can be used by the engine control unit (ECU) to adjust fuel delivery. The circuit range performance of an FRPS is determined by its design and calibration, which are critical for ensuring proper and safe functionality.
The circuit range performance of an FRPS will depend on several factors, including the size and shape of its sensing element, the type of material used in its construction, and its calibration. Generally speaking, FRPSs are designed to operate within a specified voltage range to ensure proper operation. Additionally, they must be manufactured with tight tolerances to ensure accuracy and repeatability over time.
In order to understand how well an FRPS performs in terms of circuit range performance, it is important to take into account how it functions under different conditions. For example, it should be capable of accurately measuring pressures at both low and high temperatures as well as varying pressures resulting from different engine loads or environmental conditions. Additionally, it should be able to remain accurate even after long periods of time or multiple uses. Finally, it should also be able to handle sudden changes in pressure without failing or producing false readings.
Automobile
The automobile industry is constantly changing and developing, with new technologies and components being introduced on a regular basis. One such component that has become increasingly important in recent years is the fuel rail pressure sensor. This device is used to measure the pressure of fuel in an internal combustion engine, and can be used to diagnose engine problems or improve fuel economy. In this article, we will discuss the working principle of the fuel rail pressure sensor, its advantages, how it affects circuit range performance, how it should be maintained and diagnosed, troubleshooting methods for common automobile problems and auto repair tips and techniques.
Fuel Rail Pressure Sensor
A fuel rail pressure sensor is a device that measures the pressure of fuel in an internal combustion engine. It is usually installed near the injectors on the engine’s intake manifold so that it can accurately measure the pressure of the fuel as it enters the engine. The sensor works by converting a change in fuel pressure into an electrical signal that can be read by a computerized system.
The working principle of a fuel rail pressure sensor relies on two key components: a diaphragm and a transducer. The diaphragm is connected to the intake manifold via a tube which then connects to one end of the transducer. When there is an increase or decrease in fuel pressure within the intake manifold, this causes a corresponding change in air pressure which moves the diaphragm inside the transducer. This movement is then converted into an electrical signal which can be read by a computerized system.
The advantages of using a fuel rail pressure sensor are numerous. Firstly, it provides accurate readings which can help diagnose any problems with an engine’s performance quickly and easily. Additionally, it helps to ensure optimal performance from an engine by providing accurate feedback about its current state of operation at all times. Finally, it also helps to reduce emissions as well as improve fuel economy by providing information about how much fuel is being used at any given time.
Circuit Range Performance
Circuit range performance describes how well a particular circuit performs under various conditions such as temperature changes or electrical noise interference. There are several factors which affect circuit range performance including power supply voltage levels, maximum output current levels and input impedance levels among others. In order for circuits to operate correctly within their specified range, they must be tested regularly for accuracy and reliability using specialized test equipment such as oscilloscopes or meters etc..
Testing circuit range performance involves measuring parameters such as voltage drops across components or changes in current flow through wires over time etc.. It also requires checking whether any changes in temperature or external interference are having an adverse effect on circuit performance or not. Additionally, testing should also involve periodic checks for continuity between components to ensure that all connections are intact and functioning correctly at all times.
There are several tips that can help improve circuit range performance including ensuring correct component selection based on their operating parameters such as voltage ratings etc., testing circuits regularly for accuracy and reliability using specialized equipment such as oscilloscopes etc., properly grounding components to eliminate unwanted noise interference from external sources etc., and finally ensuring that appropriate shielding techniques are employed when necessary to prevent electromagnetic interference from affecting circuit performance adversely .
Automobile Maintenance & Diagnosis
Automobile maintenance involves keeping your car in good condition so that it runs efficiently with minimal breakdowns over time due its lifetime use period . Regular maintenance includes tasks like checking oil levels , fluid levels , tire pressures , brake pads wear , spark plug connections etc . Diagnosing any faults with your car’s systems requires specialised skills which involve using specialised tools like scan tools , diagnostic software programs , multimeters etc . Some common problems associated with Fuel Rail Pressure Sensors include incorrect readings due to faulty wiring connections , incorrect calibration settings , clogged filters leading to insufficient air flow etc . To prevent recurring issues with these sensors , best practices involve routine checks for damage or wear during regular maintenance sessions , replacing faulty parts immediately when they are identified , always following manufacturer recommended installation procedures while replacing parts & adhering strictly to vehicle manufacturer’s instruction manuals while making repairs .
Troubleshooting Automobile Problems
Troubleshooting automotive problems requires patience & knowledge about how cars work so that you can identify & isolate faults quickly when they occur . Some common steps involved in troubleshooting automotive issues include performing visual inspections first & then running tests using specialised tools like scan tools & multimeters . Once faults have been identified & isolated you can then proceed with repairs accordingly . Common issues encountered during troubleshooting processes include faulty wiring connections , incorrect calibration settings or worn out parts leading to higher than expected resistance values affecting overall system functioning . To avoid recurring issues you need to always follow manufacturer recommended installation procedures while replacing parts & adhere strictly to vehicle manufacturer’s instructions while making repairs .
Auto Repair Tips & Techniques
DIY auto repair may seem intimidating at first but there are plenty of online resources available nowadays which provide detailed step-by-step instructions for most repair jobs out there . The key tool required for most DIY auto repairs jobs are basic hand tools like screwdrivers wrenches etc along with some specialized tools like timing lights & vacuum pumps depending on what type of repair job you’re undertaking . If you’re feeling unsure about tackling complex repairs yourself then professional tips from qualified mechanics may come handy too – they can provide valuable insights into specific areas where additional care needs to be taken while performing certain tasks along with other useful tips & tricks which may make your job easier when attempting difficult tasks yourself without professional help .
What is a Fuel Rail Pressure Sensor?
A fuel rail pressure sensor is a device used to measure the pressure of fuel inside the fuel rail of an internal combustion engine. The fuel pressure sensor works by measuring the amount of pressure in the fuel line, which is then used to control the amount of fuel injected into the engine. The sensor is typically located on the fuel line near the intake manifold and is attached to a wire harness that connects it to the ECU (Engine Control Unit).
What Does it Do?
The purpose of a fuel rail pressure sensor is to monitor and maintain a constant, optimal level of combustion within an engine. It does this by monitoring the pressure in the fuel line and sending a signal to the ECU when it detects that pressure has dropped or increased beyond its set range. This allows for adjustments to be made in order to maintain optimal performance from the engine.
How Does it Work?
The fuel rail pressure sensor works by measuring changes in pressure within the fuel line. When there is an increase or decrease in pressure beyond its set range, it will send a signal to the ECU indicating that there needs to be an adjustment made in order to maintain optimal performance. This can be done by either increasing or decreasing injection timing or adjusting other parameters such as air/fuel ratio, idle speed, etc.
Circuit Range Performance
The circuit range performance of a fuel rail pressure sensor is important because it determines how accurately it can detect changes in pressure within an engine’s fuel system. A good quality sensor should have a wide range circuit performance so that it can accurately detect even small changes in pressure. If a sensor has too narrow of a circuit range performance, it may not be able to detect changes in time for proper adjustments to be made and this can lead to poor engine performance.
FAQ & Answers
Q: What is a Fuel Rail Pressure Sensor?
A: A Fuel Rail Pressure Sensor is a device that measures the pressure in the fuel rail of an internal combustion engine. It helps to ensure the correct fuel delivery and performance of the engine.
Q: What are the advantages of using a Fuel Rail Pressure Sensor?
A: The advantages of using a Fuel Rail Pressure Sensor include improved fuel efficiency, better combustion, reduced emissions, and increased engine performance.
Q: What are the factors that affect Circuit Range Performance?
A: Factors that affect Circuit Range Performance include environmental conditions, load current, power supply voltage, temperature, as well as any other parameters related to circuit operation.
Q: How do you diagnose a faulty Fuel Rail Pressure Sensor?
A: To diagnose a faulty Fuel Rail Pressure Sensor, it should be tested for proper operation using specialized diagnostic equipment. In addition, any other components associated with the fuel system should be inspected for any fault codes or other signs of malfunction.
Q: What are some tips and tricks for successful Auto Repairs?
A: Some tips and tricks for successful auto repairs include having necessary tools and equipment on hand; being familiar with safety practices; having knowledge in automotive systems; researching repair techniques; and seeking professional help when needed.
In conclusion, the fuel rail pressure sensor is a crucial component of the automobile’s engine system. It is responsible for monitoring and regulating the pressure of the fuel in the fuel rail, ensuring that it is within the specified range. This allows the engine to perform optimally, providing efficient combustion and power delivery. With proper maintenance and diagnosis of this circuit range performance, vehicle owners can prevent any unexpected incidents due to fuel rail pressure issues.
Author Profile
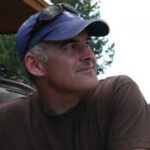
-
With more than 30 years in the bicycle industry, I have a strong background in bicycle retailing, sales, marketing and customer service. I have a passion for cycling and a dedication to excellence. As a manager, I worked diligently to increase my capabilities and responsibilities, managing up to eleven mechanics (at Palo Alto Bicycles) and later as a working partner in my own store.
As the shop owner of Spoke n’ Word Cycles in Socorro, NM, the success of the mission was my responsibility, which I pursued passionately since we opened in 2003 through the spring of 2011. I am adept at managing owned and loan inventory, preparing weekly & annual inventory statements, and managing staff. The role as managing partner also allowed me tremendous freedom. I used this personal freedom to become more deeply involved in my own advancement as a mechanic, to spearhead local trail building, and advocating for cycling both locally and regionally.
As a mechanic, I have several years doing neutral support, experience as a team mechanic, and experience supporting local rides, races, club events. I consistently strive to ensure that bicycles function flawlessly by foreseeing issues and working with the riders, soigners, coaches and other mechanics. Even with decades of experience as a shop mechanic and team mechanic, and continue to pursue greater involvement in this sport as a US Pro Mechanic, and UCI Pro Mechanic.
Latest entries
- July 26, 2023BodyFind the Best Grill for Your 2007 Toyota Tacoma – A Complete Guide
- July 26, 2023BodyUpgrade Your Ford Escape with the Best 2008 Grill – Here’s How!
- July 26, 2023Bumper Stickers, Decals And MagnetsBest Chevy 1500 Door Emblem: Upgrade Your Truck with a Stylish Emblem
- July 26, 2023Marker Light AssembliesGive Your 2008 Dodge Dakota a Makeover with the Best Grill Upgrade