Why Does My AC Compressor Clutch Keep Turning On and Off?
An AC compressor clutch is a device that engages and disengages the compressor in an air conditioning system. When the compressor clutch is engaged, the compressor is turned on, allowing it to compress and circulate refrigerant throughout the system. When the clutch is disengaged, the compressor is turned off, preventing any refrigerant from being circulated. The clutch is typically controlled by an electrical switch or a thermostat, which turns the compressor on and off as needed to maintain a desired interior temperature.
Understanding the Basic Function of an Automobile AC Compressor Clutch
An air conditioning compressor clutch is a vital component of the air conditioning system in an automobile. It is responsible for engaging and disengaging the compressor to turn the system on and off, respectively. The clutch is typically driven by a belt connected to the crankshaft, and when engaged, it allows the compressor pulley to rotate, compressing refrigerant gas and pushing it out through the system. When disengaged, it stops the compressor from spinning, preventing further cooling.
To understand how an AC compressor clutch turns on and off, we must first look at how electrical power is used to control its operation. A pressure switch is installed in-line with the compressor circuit, which monitors pressure within the system. When pressure drops below a predetermined level, it triggers a signal that turns on a relay switch to supply power to the clutch. This causes an electromagnet to engage, allowing current to flow between two contacts and allowing power to be supplied directly from the battery supply. This energizes a coil that engages the clutch and allows it to turn on or off depending on whether pressure within the system has risen or fallen below its set point.
Diagnosing a Faulty Compressor Clutch
When diagnosing an issue with an AC compressor clutch, it’s important to understand what symptoms may indicate that there’s a problem with this component of your vehicle’s air conditioning system. Common signs include: reduced airflow coming from vents; increased engine noise; increased fuel consumption due to increased strain on engine; and reduced cooling power from air conditioning unit.
Common causes of problems with compressors can range from worn out parts such as bearings or seals due to age or usage, faulty wiring or connections in electrical systems that supply power to them, low refrigerant levels due to leaks in hoses/seals or low charge levels in systems due to improper recharging/maintenance procedures being followed during servicing of units. In some cases however, issues can be caused by foreign objects such as leaves or stones becoming lodged within components which restrict airflow/movement of parts when engaged/disengaged during operation of unit itself.
When diagnosing these issues tools such as multimeters are often used which measure electrical currents running through wires so potential faults can be identified quickly without having disassemble entire units themselves. Other tools such as vacuum pumps may also be used if suspected leaks are present within system itself so they can be located accurately before repairs are attempted on them (or if necessary replaced).
Replacing a Compressor Clutch in an Automobile
Replacing an AC compressor clutch can sometimes be necessary depending upon severity of fault identified during diagnosis process discussed above. It’s important that all safety precautions are taken when attempting this kind of repair work so as not injure yourself (or others) while working on vehicle itself – use appropriate PPE (Personal Protective Equipment) such as eye protection etc when necessary while doing repairs too!
The process for replacing these components normally involves draining all refrigerant gas from existing unit before disconnecting any wires/connections associated with existing one then replacing with new part itself before reconnecting all associated parts back up again (and recharging refrigerant gas too). Depending upon make/model of vehicle involved additional parts may need replacing at same time too – for instance if bearing has failed then whole pulley assembly might need replacing alongside main clutch plate itself (which may require specialised tools). Once job is complete then test drive vehicle under controlled conditions should always be carried out ensure everything works properly before returning car back over owner/customer themselves!
Automobile Compressor Clutch Turns On and Off
Automobile compressors are a critical component of modern vehicles, as they are responsible for maintaining the proper air pressure in the air conditioning system. Unfortunately, compressor clutches can sometimes malfunction, causing them to turn on and off intermittently. This can be a major inconvenience, as it can make it difficult to maintain comfortable temperatures inside the vehicle. Fortunately, there are some steps you can take to troubleshoot this issue and get your compressor clutch working properly again.
Gathering Necessary Parts and Equipment
The first step in troubleshooting an intermittent compressor clutch is to gather the necessary parts and equipment. You will need a replacement compressor clutch, a set of wrenches or sockets, a screwdriver, electrical tape, an anti-seize compound, and a multimeter. You may also need additional supplies depending on your vehicle’s specific make and model. It is important to have all of these items on hand before starting the replacement process.
Preparing for the Replacement Process
Before beginning the replacement process, it is important to disconnect the battery cables from the battery terminals. This will ensure that there is no power running through the system during the repair process. Additionally, be sure to wear protective clothing such as gloves and goggles throughout this process to avoid any potential hazards.
Steps Involved in Replacing the Compressor Clutch
Once you have all of your supplies gathered, it is time to begin replacing your compressor clutch. The first step involves removing any components that may be obstructing access to the clutch assembly. This includes things such as hoses or wiring harnesses that may be connected to it. Once all items have been removed from around the area, you can then unbolt or unscrew any bolts or screws that are holding in place the old compressor clutch assembly.
Next, you will need to disconnect any electrical connections that may be attached to it such as wiring harnesses or plugs. Be sure not to damage these connections during removal as they will need to be reconnected later once installation is complete. Lastly, remove any remaining fasteners from around the area before carefully lifting out and discarding old compressor clutch assemblies from its housing unit.
Testing The New Compressor Clutch After Installation
Once installation is complete and all necessary connections have been made again with electrical tape or anti-seize compound where applicable , you should test out your new compressor clutch assembly by turning on your car’s AC system and setting its temperature setting higher than usual for several minutes before lowering it back down again . If everything appears working properly , then you have successfully replaced your old compressor clutch assembly .
Troubleshooting Common Issues With Automobile Compressor Clutches
If your automobile’s AC system still fails after following all steps mentioned above , then there could be other issues at hand . One common issue related with automobile compressors occurs when their electrical connections become loose over time , which can cause intermittent power issues . In this case , inspect all electrical connections around both inside and outside of your car’s AC system carefully with a multimeter , making sure they are properly connected before trying another test run . If none of these suggestions fix your problem , then consider consulting a professional technician who specializes in automotive repairs for further assistance .
FAQ & Answers
Q: What is the basic function of an automobile compressor clutch?
A: The compressor clutch is responsible for engaging and disengaging the compressor in an automobile’s air conditioning system. When engaged, the clutch connects the compressor pulley to the engine’s crankshaft and allows it to spin, which in turn compresses refrigerant gas and circulates it throughout the car’s A/C system. When disengaged, the compressor is not connected to the engine and is not able to perform its job.
Q: What are some common symptoms of a malfunctioning compressor clutch?
A: If the compressor clutch is malfunctioning, it can cause a variety of problems with your car’s air conditioning system. These include reduced cooling efficiency, increased noise from the A/C system, and an inability to cool down your car quickly. In some cases, you may also notice that your car is taking longer than usual to reach its desired temperature.
Q: What are some common causes of compressor clutch problems?
A: The most common causes of compressor clutch problems include worn out or damaged electrical connections, faulty wiring or switches, a bad ground connection, or a broken or worn out clutch plate. In some cases, inadequate lubrication can also lead to issues with your compressor clutch.
Q: What tools and processes are used to diagnose a faulty compressor clutch?
A: To diagnose a faulty compressor clutch, technicians typically use specialized tools such as voltmeters and ammeters as well as pressure gauges and thermometers. They will also need to inspect wiring diagrams for any inconsistencies that could be causing issues with the electrical connections between components in the A/C system. Finally, they may need to perform a physical inspection of all components related to the A/C system in order to identify any worn out or damaged parts that need replacing.
Q: What steps are involved in replacing a compressor clutch in an automobile?
A: Replacing a compressor clutch typically involves several steps including gathering all necessary parts and equipment; preparing for the replacement process by disconnecting electrical connections; removing any debris from around where you’ll be working; draining refrigerant lines; removing bolts that hold down the old unit; installing new bolts on new unit; reconnecting electrical connections; adding fresh refrigerant fluid; testing for proper operation; checking for leaks; refilling lubricants if needed; running through operational tests again before starting up vehicle again.
In conclusion, the automotive AC compressor clutch turns on and off in order to regulate the amount of cool air that is produced by the system. This is important for maintaining the efficiency of the AC system and ensuring that it functions optimally. The clutch engages when more cooling is needed and disengages when less cooling is needed. Understanding how this system works can help you diagnose any potential problems with your car’s AC system and ensure it runs smoothly and efficiently.
Author Profile
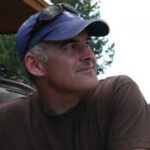
-
With more than 30 years in the bicycle industry, I have a strong background in bicycle retailing, sales, marketing and customer service. I have a passion for cycling and a dedication to excellence. As a manager, I worked diligently to increase my capabilities and responsibilities, managing up to eleven mechanics (at Palo Alto Bicycles) and later as a working partner in my own store.
As the shop owner of Spoke n’ Word Cycles in Socorro, NM, the success of the mission was my responsibility, which I pursued passionately since we opened in 2003 through the spring of 2011. I am adept at managing owned and loan inventory, preparing weekly & annual inventory statements, and managing staff. The role as managing partner also allowed me tremendous freedom. I used this personal freedom to become more deeply involved in my own advancement as a mechanic, to spearhead local trail building, and advocating for cycling both locally and regionally.
As a mechanic, I have several years doing neutral support, experience as a team mechanic, and experience supporting local rides, races, club events. I consistently strive to ensure that bicycles function flawlessly by foreseeing issues and working with the riders, soigners, coaches and other mechanics. Even with decades of experience as a shop mechanic and team mechanic, and continue to pursue greater involvement in this sport as a US Pro Mechanic, and UCI Pro Mechanic.
Latest entries
- July 26, 2023BodyFind the Best Grill for Your 2007 Toyota Tacoma – A Complete Guide
- July 26, 2023BodyUpgrade Your Ford Escape with the Best 2008 Grill – Here’s How!
- July 26, 2023Bumper Stickers, Decals And MagnetsBest Chevy 1500 Door Emblem: Upgrade Your Truck with a Stylish Emblem
- July 26, 2023Marker Light AssembliesGive Your 2008 Dodge Dakota a Makeover with the Best Grill Upgrade