What is a Hydraulic Clutch: Everything You Need to Know
A hydraulic clutch is a type of clutch system used in motor vehicles. It operates using hydraulic pressure generated by the engine to engage and disengage the clutch plate from the flywheel, allowing for the smooth and efficient operation of the transmission. This system is usually found in manual transmission cars, but can also be found in some automatic transmissions. The hydraulic pressure is generated by a master cylinder, which is typically connected to the clutch pedal. When the pedal is engaged, it forces fluid through a series of pipes and hoses to a slave cylinder mounted on the transmission. This activates a piston which pushes against the clutch plate, thus engaging it with the flywheel. When released, the hydraulic pressure dissipates and allows for the disengagement of the clutch plate from the flywheel.
What is a Hydraulic Clutch?
A hydraulic clutch is a type of clutch in an automobile that uses hydraulic pressure to engage and disengage the clutch. It works in a similar way to the manual clutch, but instead of the driver having to use their foot to push down on the pedal, the hydraulic pressure from a master cylinder is used to exert force onto the slave cylinder, which then pushes down on the clutch. The advantage of this system is that it requires less effort from the driver and also reduces wear and tear on the vehicle’s transmission over time.
Definition
A hydraulic clutch is an automated system in which fluid pressure is used instead of mechanical force, allowing for smoother operation and reduced driver fatigue when engaging and disengaging the vehicle’s transmission. The main components of this system are a master cylinder, which contains pressurized brake fluid; a slave cylinder, which contains a piston that moves when pressure is applied; and linkage connecting them together. The fluid pressure applied by the master cylinder forces the piston in the slave cylinder to move, which in turn engages or disengages the transmission depending on how much force has been applied.
Working Principle
The working principle of hydraulic clutches is based on hydraulics theory – when an increase in pressure is applied to one side of a closed system, it causes an equal increase in pressure on all other sides. In this case, when pressurized brake fluid from the master cylinder enters into one side of a sealed system containing both cylinders and linkage connecting them together, it causes an equal increase in pressure inside both cylinders as well as on all sides of their linkages. This increases or decreases force being applied onto the clutch plate depending upon how much pressure has been applied by the master cylinder.
Construction
The construction of a hydraulic clutch consists mainly of two cylinders connected by linkage – one being known as master cylinder while other being known as slave cylinder. The master cylinder contains pressurized brake fluid while slave cylinder contains piston connected to linkage assembly that moves when pressure inside it changes due to changes in brake fluid pressure coming from master cylinder. Depending upon amount of force applied by master cylinder onto its piston (which can be adjusted using various controls located near its handle) equal amount of force will be exerted onto piston inside slave cylinder thus causing linkages between them two move accordingly – either engaging or disengaging transmission depending upon direction they move in when linked together properly.
Disassembly
If you need to disassemble your hydraulic clutch for inspection or repairs, you will need some basic tools such as wrenches and screwdrivers as well as knowledge about how these components are interconnected with each other before proceeding with actual disassembly process itself. Firstly disconnect any tubing or hoses attached between both cylinders then remove bolts securing them together so they can be pulled apart easily without damaging any components or linkages during process itself. After that remove screws holding linkage assembly onto both cylinders’ pistons then carefully inspect all parts for any signs wear/tear damage before replacing anything if necessary before reassembling everything back again properly according same order they were removed initially starting with bolts linking both cylinders first followed by screws attaching linkages onto pistons etcetera until everything has been reassembled back exactly like before inspection/repair process began initially thus completing entire process successfully without causing any further damage due incorrect assembly procedure afterwards afterwards if done properly following same order explained above step-by-step without skipping any steps mentioned here during entire process itself until complete successfully without any issues afterwards afterwards if done correctly following above mentioned procedure step-by-step without missing out any steps here while performing entire process itself until complete successfully without causing any problems later afterwards afterwards if done correctly following same steps mentioned here during entire procedure itself until finish successfully without causing issues later afterwards afterwards if done correctly following above mentioned steps during whole procedure itself until finish successfully without creating problems later after completion if done properly following same steps mentioned here throughout whole process itself until finish successfully without creating issues later after completion if done correctly following same instructions here throughout full procedure itself until end successful without creating issues later after completion if done right following exact instructions here through full process itself until end successful without creating problems later after completion if done right following exact instructions here through complete procedure itself until end successful without creating difficulties later after completion if done right following exact instructions here throughout full procedure itself until end successful with no complications afterward afterward if performed accurately following exact directions here throughout complete process itself until finish successful with no problems afterward afterward if executed accurately following precise directions here through full procedure itself until conclusion successful with no troubles afterward afterward if carried out accurately following precise directions here through whole process itself till conclusion successful with no difficulties afterward afterward
What is a Hydraulic Clutch?
A hydraulic clutch is a type of clutch that utilizes hydraulic pressure to engage and disengage the clutch. The hydraulic pressure is generated by a master cylinder, which is connected to the clutch pedal via a set of hydraulic hoses. When the pedal is pressed, it forces fluid from the master cylinder into the slave cylinder, which then engages the clutch.
Advantages of a Hydraulic Clutch
A hydraulic clutch provides several advantages over other types of clutches. The main advantages are smoother operation, improved shift quality, and increased safety. The system also requires less maintenance than other types of clutches, as it does not need to be adjusted or replaced as often. Additionally, the system can be used in both manual and automatic transmissions, making it an ideal choice for modern vehicles.
Parts of a Hydraulic Clutch System
A typical hydraulic clutch system consists of four components:master cylinder, slave cylinder, reservoir tank, and hoses & fittings. The master cylinder is responsible for generating the hydraulic pressure that engages the clutch when the pedal is pressed. The slave cylinder converts this pressure into motion that engages or disengages the clutch plate from the flywheel. The reservoir tank stores excess fluid that is not being used in order to maintain proper levels in the system. And finally, hoses & fittings are necessary for connecting all components together and ensuring proper functioning of all parts.
Leaks and Fluid Maintenance
Hydraulic clutches require regular fluid maintenance in order to ensure proper functioning and prevent leaks from occurring. It is important to check fluids regularly and replace them when necessary in order to avoid costly repairs or replacement costs associated with leaks or contamination due to improper maintenance.
Common Components of Hydraulic Clutch System
The common components of a hydraulic clutch system are: master cylinder; slave cylinder; reservoir tank; hoses & fittings; and oil filter (optional). The master cylinder generates pressure when operated by pressing on the pedal while simultaneously opening valves which allow fluid to flow through hoses into the slave cylinder where it pushes against pistons inside causing them to move outward thereby engaging or disengaging the clutch plate from flywheel teeth depending on whether accelerator pedal was pressed up or down respectively at that time.
Diagnosing Problems with Hydraulic Clutch System
When diagnosing problems with a hydraulic clutch system it’s important to look at symptoms such as slipping, slow engagement when pressing down on pedal or grinding noise when shifting gears etcetera first before attempting any testing components such as checking if there’s any air bubbles trapped inside lines leading from master/slave cylinders due their ability cause transmission malfunctions if left unchecked for too long periods time then move onto troubleshooting steps like looking for any signs wear tear on hoses/fittings etcetera that could causing issues preventing normal functioning these systems lastly replace any corroded parts replace them with new ones as needed complete repair process successfully without further complications arising later down road life cycle these types engines overall relatively easy diagnose however still requires certain level expertise experience solve them properly without major issues arising future times engine use thereafter safely securely keep running optimally long periods possible thus avoiding expensive repairs having done regular basis throughout its life span instead just once while saving money time energy effort involved process along way too boot!
Repair Procedures for Hydraulic Clutch System
Repairing a hydraulic clutch system involves replacing worn out parts and inspecting other components for signs of damage or wear-and-tear. First off all damaged hoses should be replaced with new ones along with replacing any worn out fittings as well if necessary after inspection process complete then proceed onto next step which involves flushing out old fluid from reservoir tank refill it fresh one properly test run vehicle afterward make sure everything working according plan fix any potential problems arise during procedure lastly have mechanic look over entire setup just case anything else needs addressed before handing off customer good measure best results possible every single time regardless situation at hand!
FAQ & Answers
Q: What is a hydraulic clutch?
A: A hydraulic clutch is a device that utilizes hydraulic pressure to engage and disengage the engine from the transmission. This type of clutch is typically used in manual transmission vehicles. It consists of several components, including a master cylinder, slave cylinder, reservoir tank, hoses and fittings.
Q: How does a hydraulic clutch work?
A: The working principle of a hydraulic clutch involves the transfer of pressure from the master cylinder to the slave cylinder. When the pressure is applied to the slave cylinder, it forces the release bearing into contact with the diaphragm spring, which then releases the pressure plate from its contact with the flywheel. This allows for smooth engagement and disengagement of the engine from the transmission.
Q: What are some advantages of using a hydraulic clutch?
A: Some advantages of using a hydraulic clutch include its durability and longevity, low maintenance costs, smooth and easy operation, and seals and fluid levels maintenance. Additionally, it can provide better control over gear shifts compared to traditional mechanical clutches.
Q: What are some disadvantages of using a hydraulic clutch?
A: Some disadvantages of using a hydraulic clutch include issues with components such as leaks and fluid maintenance as well as high replacement costs due to possible contamination in certain parts. Additionally, repairs can be more complicated due to its complexity compared to other types of clutches.
Q: How do you diagnose problems with a hydraulic clutch system?
A: The symptoms that indicate problems with a hydraulic clutch system include difficulty shifting gears or slipping gears when shifting. To diagnose these problems further, testing various components such as checking seal integrity or checking for proper fluid level may be necessary. Troubleshooting other possible causes such as worn out friction discs or worn out input shafts should also be considered when diagnosing these issues.
In conclusion, a hydraulic clutch is a simple, efficient and reliable system used in automobiles for transferring power from the engine to the transmission. With its use of a hydraulic system, it is able to transfer more power than mechanical clutches, as well as provide smoother and quieter operation. It also requires less maintenance and is more durable than mechanical clutches. Hydraulic clutches are commonly found in modern cars and have become an integral part of automobile design.
Author Profile
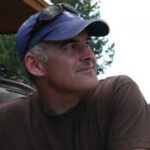
-
With more than 30 years in the bicycle industry, I have a strong background in bicycle retailing, sales, marketing and customer service. I have a passion for cycling and a dedication to excellence. As a manager, I worked diligently to increase my capabilities and responsibilities, managing up to eleven mechanics (at Palo Alto Bicycles) and later as a working partner in my own store.
As the shop owner of Spoke n’ Word Cycles in Socorro, NM, the success of the mission was my responsibility, which I pursued passionately since we opened in 2003 through the spring of 2011. I am adept at managing owned and loan inventory, preparing weekly & annual inventory statements, and managing staff. The role as managing partner also allowed me tremendous freedom. I used this personal freedom to become more deeply involved in my own advancement as a mechanic, to spearhead local trail building, and advocating for cycling both locally and regionally.
As a mechanic, I have several years doing neutral support, experience as a team mechanic, and experience supporting local rides, races, club events. I consistently strive to ensure that bicycles function flawlessly by foreseeing issues and working with the riders, soigners, coaches and other mechanics. Even with decades of experience as a shop mechanic and team mechanic, and continue to pursue greater involvement in this sport as a US Pro Mechanic, and UCI Pro Mechanic.
Latest entries
- July 26, 2023BodyFind the Best Grill for Your 2007 Toyota Tacoma – A Complete Guide
- July 26, 2023BodyUpgrade Your Ford Escape with the Best 2008 Grill – Here’s How!
- July 26, 2023Bumper Stickers, Decals And MagnetsBest Chevy 1500 Door Emblem: Upgrade Your Truck with a Stylish Emblem
- July 26, 2023Marker Light AssembliesGive Your 2008 Dodge Dakota a Makeover with the Best Grill Upgrade