How to Troubleshoot a Knock Sensor 1 Circuit Bank 1 or Single Sensor
Knock Sensor 1 Circuit Bank 1 or Single Sensor is a type of engine monitoring system designed to detect knocking or pinging in automobile engines. This system uses a single knock sensor mounted on the engine block to detect vibrations created by pre-ignition or detonation within the combustion chamber. When activated, the sensor sends an electrical signal to the ECU (Engine Control Unit), which in turn adjusts the fuel and timing settings in order to prevent further damage from occurring. This type of system is commonly used in modern vehicles with gasoline engines, and can be beneficial for both performance and longevity.
Definition
A knock sensor is a type of sensor found in an automobile, which is used to detect abnormal combustion in the engine. It does this by detecting changes in the pressure wave created by combustion and then sending a signal to the engine control unit (ECU) to adjust the timing and fuel injection accordingly. The knock sensor is usually located near the spark plug or spark plug wire on modern engines.
Functions
The primary function of a knock sensor is to detect knocking, or abnormal combustion that can occur when an engine is running too hot or too lean. When this occurs, it can cause damage to internal components such as pistons, rings and valves. The knock sensor detects this knocking and sends a signal to the ECU, which then adjusts the timing and fuel injection accordingly in order to prevent further damage from occurring.
The knock sensor also helps improve fuel economy by enabling the ECU to adjust timing and fuel injection for optimum performance. This means that when an engine is running at its most efficient level, less fuel is being consumed. This leads to improved fuel economy and reduced emissions from the vehicle.
Types
There are two main types of knock sensors: single-sensor and multi-sensor systems. Single-sensor systems are typically found on older vehicles where only one sensor is used for monitoring combusion conditions. Multi-sensor systems are more commonly found on modern vehicles where several sensors are used to monitor different cylinders simultaneously.
Location
Knock sensors can be located anywhere between the spark plug or spark plug wire on modern engines, depending on their make and model. However, they are most commonly located near the intake manifold on inline 4-cylinder engines or near each individual cylinder head bank on V6 or V8 engines (known as Knock Sensor 1 Circuit Bank 1 or Single Sensor). On most vehicles, they will be connected directly to the ECU via a wiring harness or through an onboard diagnostics port (OBD).
Automobile: Knock Sensor Circuit Bank 1 or Single Sensor
An automobile knock sensor is an electronic device used in modern cars to detect engine pre-ignition or detonation. When the engine experiences a pre-ignition, the knock sensor detects a vibration or shock wave that is generated by the combustion event, and then sends an electronic signal to the engine control unit (ECU) to adjust the ignition timing accordingly. The ECU then adjusts the timing to prevent engine damage from occurring due to pre-ignition.
Electronic Signals Generated by Knock Sensor
The knock sensor produces two types of signals: voltage and frequency. The voltage output from the knock sensor is typically in the range of 0.4V – 4V, and is directly proportional to the amount of pre-ignition occurring in the engine. The frequency output is typically between 200 Hz and 2000 Hz, and is directly related to how often pre-ignition occurs. Both signals are used by the ECU to adjust ignition timing in order to reduce or eliminate pre-ignition events.
Effects of Detonation on Knock Sensor Performance
When detonation or pre-ignition occurs, it causes an increase in pressure inside of an engine’s cylinders which can cause serious damage if left unchecked. In order for a knock sensor circuit to properly detect these pressures, it needs to be able to sense vibrations that occur as a result of pressure waves created by detonation. If too much pressure builds up inside of a cylinder, it can cause permanent damage such as warped pistons or broken rings that can lead to higher than normal levels of oil consumption or exhaust gas leakage.
What is a Knock Sensor Circuit in an Automobile?
A knock sensor circuit in an automobile consists of several components including transducers, amplifiers and filters which all work together to sense vibrations caused by detonation events within an engine’s cylinders. The transducers are mounted directly onto each cylinder head and are designed to pick up any vibrations produced during combustion events while amplifiers increase their sensitivity so that even small amounts of detonation can be detected by the ECU. Finally, filters are used to remove any unwanted noise from other sources such as exhaust systems so that only detonation related signals are sent back for analysis by the ECU.
What are the Different Types of Knock Sensor Circuits?
There are two main types of knock sensors circuits used in modern automobiles: single-sensor circuits and dual-sensor circuits. Single-sensor circuits use only one transducer mounted onto each cylinder head which produces both voltage and frequency outputs when there is pre-ignition occurring inside its chamber. Voltage outputs range between 0.4V – 4V while frequency outputs range between 200 Hz – 2000 Hz depending on how much detonation occurs within each cylinder head being monitored by these sensors circuit banks 1or single sensors . Dual-sensor circuits use two transducers mounted onto each cylinder head which produce both voltage and frequency outputs when there’s pre-ignition occurring inside its chamber but with greater accuracy compared with single sensor circuits due to having more data points available for analysis by the ECU
FAQ & Answers
Q: What is a knock sensor?
A: A knock sensor is a type of sensor found in an automobile engine. It is used to detect the onset of detonation in the engine, which can cause engine damage if left unchecked. The knock sensor monitors vibrations and changes in air pressure to detect when the engine is about to detonate.
Q: What is a knock sensor circuit?
A: A knock sensor circuit is an electronic system designed to monitor and detect changes in the engine’s vibration and air pressure. It consists of transducers, amplifiers, filters, and other components that work together to read the data from the knock sensor. The data is then sent to the vehicle’s ECU (engine control unit) for further analysis.
Q: What are the different types of knock sensor circuits?
A: There are two main types of knock sensor circuits – single-sensor circuits and multi-sensor circuits. Single-sensor circuits have one transducer that reads data from the knock sensor, while multi-sensor circuits have multiple transducers that read data from multiple sensors.
Q: What are the functions of a knock sensor?
A: The main function of a knock sensor is to detect when an engine is about to detonate due to pre-ignition or abnormal combustion. When this occurs, it sends an electronic signal to the vehicle’s ECU (engine control unit), which then adjusts certain parameters in order to reduce or eliminate detonation. This helps prevent damage caused by detonation, such as piston failure or cylinder head cracking.
Q: Where is the knock sensor located on an automobile?
A: The exact location of a vehicle’s knock sensor will vary depending on make and model. Generally speaking, it will be located near or on top of the cylinder head or intake manifold assembly. The exact location can be found in the owner’s manual for your specific vehicle.
In conclusion, a Knock Sensor 1 Circuit Bank 1 or single sensor is an essential component of an automobile engine that helps to detect and monitor knock events in the engine. It can help to optimize engine performance and prevent knock-related damage. By monitoring the pressure waves created by knocking, the Knock Sensor can detect these events and alert the engine controller accordingly. This allows for better control of fuel/air mixture, timing, and other parameters to ensure safe operation of the engine.
Author Profile
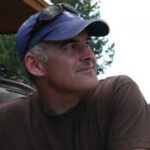
-
With more than 30 years in the bicycle industry, I have a strong background in bicycle retailing, sales, marketing and customer service. I have a passion for cycling and a dedication to excellence. As a manager, I worked diligently to increase my capabilities and responsibilities, managing up to eleven mechanics (at Palo Alto Bicycles) and later as a working partner in my own store.
As the shop owner of Spoke n’ Word Cycles in Socorro, NM, the success of the mission was my responsibility, which I pursued passionately since we opened in 2003 through the spring of 2011. I am adept at managing owned and loan inventory, preparing weekly & annual inventory statements, and managing staff. The role as managing partner also allowed me tremendous freedom. I used this personal freedom to become more deeply involved in my own advancement as a mechanic, to spearhead local trail building, and advocating for cycling both locally and regionally.
As a mechanic, I have several years doing neutral support, experience as a team mechanic, and experience supporting local rides, races, club events. I consistently strive to ensure that bicycles function flawlessly by foreseeing issues and working with the riders, soigners, coaches and other mechanics. Even with decades of experience as a shop mechanic and team mechanic, and continue to pursue greater involvement in this sport as a US Pro Mechanic, and UCI Pro Mechanic.
Latest entries
- July 26, 2023BodyFind the Best Grill for Your 2007 Toyota Tacoma – A Complete Guide
- July 26, 2023BodyUpgrade Your Ford Escape with the Best 2008 Grill – Here’s How!
- July 26, 2023Bumper Stickers, Decals And MagnetsBest Chevy 1500 Door Emblem: Upgrade Your Truck with a Stylish Emblem
- July 26, 2023Marker Light AssembliesGive Your 2008 Dodge Dakota a Makeover with the Best Grill Upgrade