Resolving a Circuit Low with a Fuel Level Sensor
A fuel level sensor is an electronic device that measures the amount of fuel remaining in a vehicle’s fuel tank. The sensor typically uses a variable resistor to measure the level of fuel, and it sends an electrical signal to the vehicle’s computer system indicating the amount of fuel remaining in the tank. If a circuit low is detected in the fuel level sensor, it means that there is either a problem with the sensor itself or with the wiring connected to it. This could be caused by corrosion or other damage to the connections between the sensor and its wiring harness, as well as a malfunctioning sensor. In order to diagnose and repair this problem, it is important to first inspect all of the wiring around the fuel tank, ensuring that all connections are secure and free from corrosion or other damage. If no problems are found, then the next step would be to test and replace any faulty components of the fuel level sensor circuit.
Checking Wiring Connections
When troubleshooting a low fuel level sensor A circuit, it is important to first check the wiring connections. Any short circuits or corrosion that may be present should be identified and addressed. If any of these issues are found, they should be repaired or replaced in order to restore proper functioning of the fuel level sensor A circuit.
It is also important to ensure that all connections are securely fastened and that all wires have a strong seal so that no air leaks occur. It is also a good idea to inspect for any wire damage or fraying, as this can cause further electrical issues.
Checking the Fuel Level Sensor
The next step in troubleshooting a low fuel level sensor A circuit is to inspect the fuel level sensor itself. This component should be inspected for any signs of wear or damage, as well as any debris that could potentially interfere with its functioning. If any of these issues are found, they should be addressed promptly in order to restore proper performance of the fuel level sensor A circuit.
Additionally, it is important to make sure the fuel level sensor has been properly calibrated and that it is providing accurate readings of the current fuel levels. If these readings are not within an acceptable range, then further adjustment may be necessary before troubleshooting can continue.
Verifying Instrument Cluster Functionality
Once the wiring connections and fuel level sensor have been inspected and verified, it is important to verify that the instrument cluster is functioning properly. This can be done by using a multimeter or other diagnostic tool to check for proper voltage readings from each component in the instrument cluster.
If any discrepancies are found or if some components appear to not be working correctly, then further inspection will need to take place in order to identify and address any underlying issues with the instrument cluster circuitry.
Testing Power Supply Voltage
The final step in troubleshooting a low fuel level sensor A circuit is testing the power supply voltage for accuracy. This can be done by using a multimeter or other diagnostic tool to measure voltage at various points throughout the vehicle’s electrical system. It is important to make sure the power supply voltage remains within an acceptable range so as not to cause further damage or disruption within other components of the vehicle’s electrical system.
If there are any discrepancies found during this testing phase, then further inspection will need to take place in order to identify and address any underlying issues with power supply circuitry before further troubleshooting can continue on the low fuel level sensor A circuit issue.
Measuring the Resistance of the Fuel Level Sensor
The resistance of a fuel level sensor is a critical factor in determining the accuracy of the readings. To accurately measure the resistance of a fuel level sensor, it is necessary to inspect the wiring harness that connects it to the instrument cluster. This should be done to ensure that there are no breaks or loose connections in any of the wires. If any faults are found, they should be repaired before attempting to measure the resistance.
Once it has been established that all connections are secure, a multimeter can then be used to measure the resistance of each wire connected to the fuel level sensor. The readings should match up with expected values for each wire, and any discrepancies could indicate an issue with either the wiring or the fuel level sensor itself.
Establishing an Electric Connection with the Instrument Cluster
In order for a fuel level sensor circuit low reading to be properly diagnosed and corrected, it is necessary to establish an electric connection between it and an instrument cluster. This connection allows data from both components to be transmitted back and forth so that readings can be interpreted accurately.
To begin this process, all wiring harnesses should first be inspected for any signs of damage or corrosion. If any faults are found in either component’s wiring harnesses they must be repaired before attempting to establish an electric connection between them. Once all connections have been verified as secure, then a voltage meter can be used to test for continuity between both components. This will confirm whether or not power is being sent between them correctly and allow for further diagnosis if there are any issues present in either component’s circuitry.
Verifying the Voltage Output of the Power Supply
In order for a fuel level sensor circuit low reading to be accurately diagnosed and corrected, it is also important to verify that voltage output from its power supply is within acceptable parameters. This can be done by using a multimeter and measuring voltage output at each point on its circuit board where voltage is expected to flow through in order for it operate correctly. Any discrepancies between expected values and actual readings could indicate either a faulty power supply or wiring issue which must then be addressed before proceeding further with diagnosis and repair work related to a circuit low error code on this component’s system board diagnostics report.
Common Causes of Low Fuel Level Sensor A Circuit Malfunction
Low fuel level sensor A circuit malfunctions can have many potential causes, some of which include faulty or damaged wiring connections, defective or degraded fuel level sensors, poor installation practices during production line assembly processes, as well as environmental factors such as moisture seepage into sensitive areas on its system board resulting in corrosion damage over time which can disrupt signal flow between components within its circuitry network causing intermittent issues with its functionality when exposed to extreme temperatures outside of normal operating conditions for extended periods of time without proper insulation protection from these elements during use outdoors etc… In these cases it may become necessary either replace individual components within its system board circuitry network or entirely replace this device altogether depending on severity of damage incurred due its exposure environmental extremes experienced on regular basis over extended periods without sufficient protection from such elements when operated outdoors etc…
FAQ & Answers
Q: What could cause a low fuel level sensor A circuit?
A: Possible causes of a low fuel level sensor A circuit include poor wiring connections, a faulty fuel level sensor, a faulty instrument cluster, or low power supply voltage.
Q: How can I troubleshoot a low fuel level sensor A circuit?
A: Troubleshooting a low fuel level sensor A circuit involves inspecting wiring connections for short circuits and corrosion, measuring the resistance of the fuel level sensor, establishing an electric connection with the instrument cluster, and verifying the voltage output of the power supply.
Q: What are some common causes of a low fuel level sensor A circuit malfunction?
A: Common causes of a low fuel level sensor A circuit malfunction include faulty or damaged wiring connections and defective or degraded fuel level sensors.
Q: How can I check wiring connections?
A: To check wiring connections, inspect the wiring harness for short circuits and corrosion. Make sure all wires are securely connected and that no wires have been damaged due to wear and tear or external factors.
Q: How do I measure the resistance of the fuel level sensor?
A: To measure the resistance of the fuel level sensor, use an ohmmeter to measure resistance across terminals on the connector. Make sure to note any abnormal readings that may indicate a defective or degraded fuel level sensor.
In conclusion, the fuel level sensor circuit is an important component of an automobile’s fuel system. If a vehicle’s fuel level drops to a low level, the circuit will alert the driver with a warning light to remind them to refuel. The circuit is composed of a number of components including a resistor, capacitor and transistor which all work together to detect changes in voltage and alert the driver when the fuel level drops too low. With proper maintenance, this circuit should provide reliable service and keep drivers safe on the road.
Author Profile
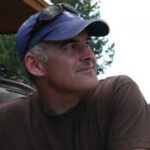
-
With more than 30 years in the bicycle industry, I have a strong background in bicycle retailing, sales, marketing and customer service. I have a passion for cycling and a dedication to excellence. As a manager, I worked diligently to increase my capabilities and responsibilities, managing up to eleven mechanics (at Palo Alto Bicycles) and later as a working partner in my own store.
As the shop owner of Spoke n’ Word Cycles in Socorro, NM, the success of the mission was my responsibility, which I pursued passionately since we opened in 2003 through the spring of 2011. I am adept at managing owned and loan inventory, preparing weekly & annual inventory statements, and managing staff. The role as managing partner also allowed me tremendous freedom. I used this personal freedom to become more deeply involved in my own advancement as a mechanic, to spearhead local trail building, and advocating for cycling both locally and regionally.
As a mechanic, I have several years doing neutral support, experience as a team mechanic, and experience supporting local rides, races, club events. I consistently strive to ensure that bicycles function flawlessly by foreseeing issues and working with the riders, soigners, coaches and other mechanics. Even with decades of experience as a shop mechanic and team mechanic, and continue to pursue greater involvement in this sport as a US Pro Mechanic, and UCI Pro Mechanic.
Latest entries
- July 26, 2023BodyFind the Best Grill for Your 2007 Toyota Tacoma – A Complete Guide
- July 26, 2023BodyUpgrade Your Ford Escape with the Best 2008 Grill – Here’s How!
- July 26, 2023Bumper Stickers, Decals And MagnetsBest Chevy 1500 Door Emblem: Upgrade Your Truck with a Stylish Emblem
- July 26, 2023Marker Light AssembliesGive Your 2008 Dodge Dakota a Makeover with the Best Grill Upgrade